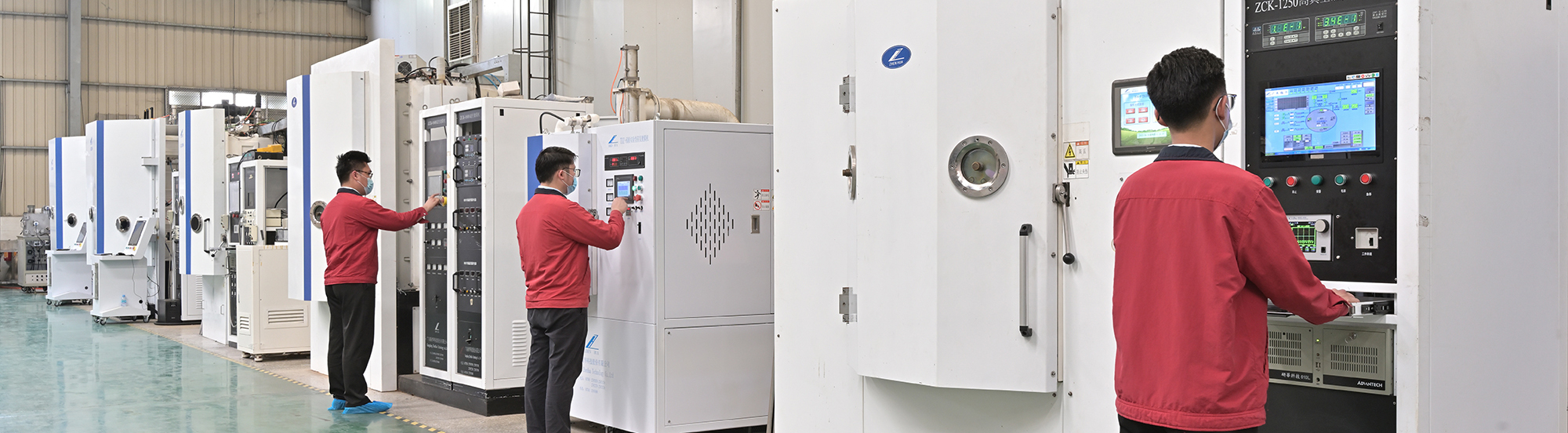
PVD在CMS智能后視鏡中的應(yīng)用
智能后視鏡作為現(xiàn)代汽車智能化的重要組成部分,不僅需具備傳統(tǒng)鏡面的反射功能,還需集成攝像頭、顯示屏、觸控操作等模塊。這些功能對(duì)鏡面涂層的導(dǎo)電性、透光性、耐磨性及耐候性提出了更高要求。磁控濺射鍍膜技術(shù)憑借其高精度、高可控性和多功能性,成為實(shí)現(xiàn)智能后視鏡高性能鍍層的核心技術(shù)之一。
一.磁控濺射鍍膜工藝原理
磁控濺射(Magnetron Sputtering)是一種高效的物理氣相沉積(PVD)技術(shù)。該工藝通過在真空環(huán)境中引入惰性氣體(如氬氣),在電場(chǎng)和磁場(chǎng)的作用下,使靶材(如金屬或氧化物)原子濺射并沉積到基材表面,形成均勻、致密的鍍膜層。相比傳統(tǒng)的蒸發(fā)鍍膜,磁控濺射具有膜層均勻性高、附著力強(qiáng)、工藝穩(wěn)定等優(yōu)勢(shì),廣泛應(yīng)用于光學(xué)、電子和裝飾等領(lǐng)域。
二.智能后視鏡中的關(guān)鍵鍍膜應(yīng)用
1.防反射與高反射膜:光學(xué)性能優(yōu)化
防反射膜:通過交替濺射高折射率(如TiO?)和低折射率(如SiO?)材料的多層膜,減少鏡面反射光干擾,增強(qiáng)顯示屏的可見性38。
高反射膜:在鏡面背側(cè)濺射鋁或銀膜,反射率可達(dá)95%以上,確?;A(chǔ)光學(xué)性能的同時(shí)兼容攝像頭成像需求。
2.耐磨與耐腐蝕保護(hù)層
智能后視鏡顯示屏經(jīng)常暴露在陽光、風(fēng)沙等環(huán)境中,易受刮擦影響。磁控濺射可以形成高硬度的耐磨膜層,提高屏幕耐用性,延長使用壽命。
3.防水防污膜層
車載攝像頭容易受到雨水、灰塵等環(huán)境因素影響,導(dǎo)致視野模糊。通過磁控濺射工藝,可在攝像頭外鏡片上鍍制疏水疏油膜,使水滴快速滑落,減少污漬殘留,從而保持長期清晰成像。
4.紅外增強(qiáng)鍍膜
夜間或低光環(huán)境下,CMS系統(tǒng)往往依賴紅外光輔助成像。磁控濺射工藝可在攝像頭濾光片上鍍制特定的紅外增透膜,提高對(duì)紅外光的敏感度,從而增強(qiáng)夜視效果,使夜間駕駛更安全。
三.技術(shù)優(yōu)勢(shì)
1.高精度與均勻性
磁控濺射鍍膜技術(shù)能夠制備厚度均勻、致密性高的薄膜,膜層附著力強(qiáng),且可實(shí)現(xiàn)納米級(jí)精度的厚度控制。
2.材料適用性廣
該技術(shù)可沉積金屬、合金、陶瓷、氧化物等多種材料,尤其適合高熔點(diǎn)或低蒸汽壓材料的鍍膜。
3.環(huán)保與節(jié)能
相比傳統(tǒng)濕法電鍍,磁控濺射無需使用化學(xué)試劑,避免了廢水、廢氣排放,符合綠色制造趨勢(shì)。
4.適應(yīng)復(fù)雜基材
針對(duì)曲面玻璃等異形基材,銀度節(jié)能推出的擺動(dòng)式靶材裝置通過動(dòng)態(tài)調(diào)整濺射角度,解決了傳統(tǒng)工藝中的膜層厚度不均問題。
四.未來發(fā)展方向
為了應(yīng)對(duì)這些挑戰(zhàn),磁控濺射技術(shù)正在向更高效、更智能的方向發(fā)展:
1.大面積鍍膜設(shè)備:研發(fā)適用于更大基板尺寸的磁控濺射生產(chǎn)線,滿足汽車玻璃、光學(xué)顯示等行業(yè)的批量需求。
2.提高沉積速率:開發(fā)高功率脈沖磁控濺射(HiPIMS)等新技術(shù),提高鍍膜速率的同時(shí)保持高膜層質(zhì)量。
3.優(yōu)化材料利用率:改進(jìn)靶材設(shè)計(jì),如旋轉(zhuǎn)靶、非平面靶,以提高濺射效率,減少材料浪費(fèi)。
4.提升自動(dòng)化水平:引入智能監(jiān)控系統(tǒng),實(shí)現(xiàn)鍍膜過程的實(shí)時(shí)監(jiān)測(cè)與參數(shù)優(yōu)化,提高產(chǎn)能和穩(wěn)定性。
五.振華真空大平面光學(xué)鍍膜生產(chǎn)線
大平面光學(xué)鍍膜生產(chǎn)線
設(shè)備優(yōu)勢(shì):
1.可量產(chǎn)2m x 3m超大尺寸光學(xué)玻璃
2.自動(dòng)化程度高:機(jī)械手銜接上下工序,實(shí)現(xiàn)流水線作業(yè)
3.產(chǎn)能大,能耗低:產(chǎn)量最高可達(dá)50㎡/h
5.膜層性能優(yōu)越:多重精密光學(xué)膜疊加,最多可達(dá)14層,鍍膜重復(fù)性好
應(yīng)用范圍:智能后視鏡/車載中控面板/觸控屏玻璃蓋板/攝像頭玻璃/光學(xué)鏡頭等。
——本文由真空鍍膜機(jī)廠家振華真空發(fā)布。